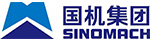
文章出處:知識中心 網責任編輯: 洛陽軸承 閱讀量: 發(fā)表時間:2022-02-15 17:36:05
針對滾動軸承空心滾子內孔去氧化皮的難題,采用粒度為46,220目的碳化硅黏彈性流體磨料,對擠壓軋機軸承的空心滾子進行去除內孔氧化皮試驗,結果表明:利用磨料流加工方法可以有效去除空心滾子內孔的氧化皮;在相同的磨料流加工參數下,采用不同粒度的碳化硅磨??色@得不同的加工表面,加工表面應與所用的碳化硅磨粒相匹配,氧化皮較厚的加工表面應分階段進行加工,以便實現良好的氧化皮去除效果。
1、概述
目前,應用于軋機領域的大型滾動軸承由于在鋼材軋制過程中承受載荷大,導致軸承中主要承載的滾動體受力較大。為提高軸承承載能力,多選用空心滾子,通過支柱穿過空心滾子,并與保持架采用焊接的方式連接。支柱焊接保持架在重載工況下會出現滾動體或滾道表面的疲勞失效,除保持架鉆孔不齊和焊接應力造成的支柱偏斜外,與空心滾子連接的支柱孔內表面氧化皮去除不凈引起的剝落、表面磨損也會造成軸承疲勞失效。為減少滑動摩擦對滾子的損害,通常采用噴砂或手工方法去除空心滾子內孔氧化皮,但加工效率低,很難實現均勻去除,還對工人和環(huán)境造成較為惡劣的影響。
磨料流加工方法最早由美國研究者提出,該方法采用液壓機作為動力傳動系統(tǒng),單向或雙向反復擠壓黏彈性的流體磨料,使磨料在壓力作用下快速與工件的表面產生摩擦,從而實現對工件表面的磨拋,其加工原理如圖1所示。本文主要應用磨料流技術對軸承空心滾子內孔表面的氧化皮進行去除試驗。
1—夾具;2—上料缸;3—工件;4—黏彈性磨料;5—下料缸;6—擠壓活塞。
圖1 磨料流加工法的加工原理
Fig.1 Machining principle of abrasive flow machining method
磨粒作為磨料流加工的磨削介質,其粒度和濃度對氧化皮的去除效果有著重要影響,在進行磨料流壓差調節(jié)及截面匹配等試驗前,應根據不同的加工表面選擇合適的磨粒。文獻[8-10]選用不同粒度和濃度的黏彈性磨料對不同材質工件表面的氧化皮進行擠壓去除,磨料流的磨粒特性研究結果表明:不同加工方法獲得的工件表面應該選擇不同粒度的磨粒對氧化皮進行去除;采用磨料流加工法對于電火花加工后在工件表面所生成氧化皮的去除效果最佳。另外,隨著循環(huán)加工次數的增多,表面粗糙度Rα變化趨于恒定。
2、試驗
針對某特大型軋機軸承空心滾子在熱處理后滾子內孔氧化皮去除難的問題,利用自主研發(fā)的磨料流機床進行研磨試驗。該磨料流加工設備的加工原理如圖2所示,磨料流加工主要依靠2個液壓缸對稱往復擠壓半固態(tài)流體磨料介質,穿過由工件與夾具形成的密封流道,磨料與工件表面產生相對摩擦,從而實現磨拋加工。加工過程中利用上下壓板將工件固定,通過調整上下壓板的間距改變工件的數量,該設備一次最多可以加工7個型號相同的工件。
1—下液壓缸;2—下磨料缸;3—下壓板;4—7個工件;5—上壓板;6—磨料;7—上液壓缸;8—活塞;9—上磨料缸;10—液壓站。
圖2 磨料流設備及原理示意圖
Fig.2 Diagram of abrasive flow equipment and principle
空心滾子試樣材料為GCr15,尺寸為φ60 mm×φ18 mm×60 mm。由于在熱處理過程保護氣氛的作用下,熱處理后可以清晰地看到厚薄不均勻的黑色氧化皮,且去除困難??招臐L子線切割后主要尺寸及內孔表面的氧化皮如圖3所示。
圖3 熱處理后空心滾子的主要尺寸及內孔表面
Fig.3 Main sizes and bore surface of hollow roller after heat treatment
磨料流加工常用磨料有碳化硅、立方氮化硼、氧化鋁和金剛砂?;谏鲜?種磨料的材料去除特性,選擇碳化硅黏彈性磨料作為磨削介質進行試驗。為驗證磨料粒度對加工表面的加工效果,選擇220目(粒徑65 μm)和46目(粒徑330 μm)的碳化硅磨料,在用磨料擠壓空心滾子時,采用“穿膛過”式的擠壓方式,且不設置背壓(在工件末端處不設置與磨料流流動方向相反的壓力)。通過調節(jié)夾具的開口壓力使推程和回程的擠壓壓力皆為6.5 MPa,背壓壓力為2.0 MPa,磨料完成1次往復運動需18 s,循環(huán)擠壓設為50 次,總加工時間為15 min。加工完成后利用線切割機將空心滾子切開進行觀察。
3、結果與討論
3.1 磨料粒度對氧化皮去除效果的影響
采用220目和46目的碳化硅黏彈性磨料去除氧化皮的對比效果如圖4所示:采用粒度較細的220目碳化硅磨料時,磨料流的磨料粒子呈漿體狀而無法識別個體磨料,加工后工件表面仍有少量氧化皮殘留,且分布不均勻;采用粒度較粗的46目碳化硅磨料時,磨料流的磨料粒子幾乎肉眼可見,加工后氧化皮已經完全去除,漏出金屬表面本體。由于磨料流是一種柔性微刃切削,當碰到硬點時會主動退讓,當目數較小且被拋光表面較粗糙時,磨粒從表面滑過并不起切削作用或切削深度微小,而選用粒度較粗的磨粒,在表面可以充分地進行滑擦、耕犁、翻滾,完成切削過程,氧化皮的去除效果好。
圖4 不同粒度的磨料對空心滾子內孔表面氧化皮的去除效果
Fig.4 Removal effect of abrasives with different particle sizes on oxide films on bore surface of hollow roller
3.2 內孔表面粗糙度的建模分析
在磨料流加工中,假定工件內表面輪廓均勻,初始表面粗糙度為Ra0,并且磨料在壓力作用下沿工件內孔的軸線方向往復移動,劃痕方向上的峰谷粗糙度Rt0與算術平均表面粗糙度Ra比值恒定。假定Rai為第i次加工后獲得的內孔表面粗糙度,其模型可由(1)式計算,即
式中:N為單位面積作用的磨料的磨粒數量;ls為加工行程;Rw為磨料流的半徑;Rc為磨料缸的內徑;dg為磨粒的直徑;t為材料去除深度。由(1)式可知當工件內表面較粗糙時,材料去除深度較大,應采用較大的磨粒直徑。若想獲得高精度內表面,磨粒直徑應隨工件表面粗糙度的變化及時調整,采用多階段磨料流加工,根據每個加工階段后工件表面粗糙度,逐漸減小磨料直徑。
3.3 磨料流加工對內孔表面粗糙度的影響
表面粗糙度作為表面完整性的一個重要指標,對產品質量起著決定性作用。通過試驗可以看出磨料流加工時,游離態(tài)的碳化硅磨粒對GCr15軸承鋼滾子內表面粗糙度具有很好的改善效果。利用接觸式探針對磨料流加工后的滾子內孔表面粗糙度進行測量,結果如圖5所示:隨著氧化皮的去除,內孔表面粗糙度Ra值均明顯下降。內孔表面經過15 min磨料流加工后,采用46目磨粒時,Ra由初始的4.60 μm降至1.00 μm;而采用220目的磨粒時,Ra僅降至1.63 μm。由此可見,選擇合適的磨粒目數對表面的加工精度和加工效率起到至關重要的作用。
圖5 磨料流加工前后滾子內孔表面粗糙度
Fig.5 Surface roughness of bore surface of roller before and after abrasive flow machining
3.4 進出口處的過拋現象
在上述無背壓的“穿膛過”磨粒流加工條件下,將加工后的工件線切割開,可以明顯看出進出口處的尺寸d1,大于中間區(qū)域的尺寸d0,并形成“喇叭口”。出現該結果的主要原因是由于黏彈性磨料在出口處的突然擠入與釋放時形成的擠壓壓力過大,從而在工件兩端出現嚴重的過拋現象,嚴重影響空心滾子的尺寸。為避免“喇叭口”的形成,應該控制進出口的壓差,使磨粒流在加工過程中實現均勻的擠壓運動。因此,在擠壓過程中對磨粒流施加一個回程壓力,即背壓P2與“穿膛過”式(背壓P2為零)的情況相比,在擠壓過程中增加磨料流回程壓力,可以降低壓力在進出口處的突變,實現進出口處壓力的小壓差調節(jié),從而有效抑制“喇叭口”的形成,其原理如圖6所示。
式中:N為單位面積作用的磨料的磨粒數量;ls為加工行程;Rw為磨料流的半徑;Rc為磨料缸的內徑;dg為磨粒的直徑;t為材料去除深度。由(1)式可知當工件內表面較粗糙時,材料去除深度較大,應采用較大的磨粒直徑。若想獲得高精度內表面,磨粒直徑應隨工件表面粗糙度的變化及時調整,采用多階段磨料流加工,根據每個加工階段后工件表面粗糙度,逐漸減小磨料直徑。
3.3 磨料流加工對內孔表面粗糙度的影響
表面粗糙度作為表面完整性的一個重要指標,對產品質量起著決定性作用。通過試驗可以看出磨料流加工時,游離態(tài)的碳化硅磨粒對GCr15軸承鋼滾子內表面粗糙度具有很好的改善效果。利用接觸式探針對磨料流加工后的滾子內孔表面粗糙度進行測量,結果如圖5所示:隨著氧化皮的去除,內孔表面粗糙度Ra值均明顯下降。內孔表面經過15 min磨料流加工后,采用46目磨粒時,Ra由初始的4.60 μm降至1.00 μm;而采用220目的磨粒時,Ra僅降至1.63 μm。由此可見,選擇合適的磨粒目數對表面的加工精度和加工效率起到至關重要的作用。
圖6 小壓差與無壓差調節(jié)拋光出口處對比分析
Fig.6 Comparative analysis of AFM with a small differential pressure and no differential pressure adjustment at polishing outlet
為進一步驗證背壓下磨料流對空心滾子內孔進口與出口氧化皮的擠壓去除效果,分別將背壓設定為0,2.0 MPa進行20次循環(huán)的磨料流加工。試驗后測量空心滾子的端口處直徑,結果如圖7所示:采用無背壓“穿膛過”式磨料流加工后的徑口直徑為20.112 mm,而采用2.0 MPa背壓后的徑口直徑為19.120 mm。為確保加工后滾子內孔的尺寸,在加工過程對磨料流施加適當的背壓,可有效抑制過拋現象。
圖7 無背壓及背壓調節(jié)下端口倒圓情況
Fig.7 Rounding of port without back pressure and back pressure adjustment
3.5 加工效果對比
基于上述試驗結果,將磨料流去氧化皮方法與傳統(tǒng)手工和噴砂去氧化皮進行對比,結果見表1,采用磨料流加工方法去除氧化皮的經濟性和加工質量均明顯優(yōu)于其他2種,且磨料流加工法更環(huán)保,但加工效率略低于其他2種。
表1 手工、噴砂與磨料流去除氧化皮成本和加工效率對比
Tab.1 Comparison of costs and machining efficiency of manual,sandspray and abrasive flow to remove oxide films
4、結論
針對空心滾子內孔表面氧化皮的去除難題,利用磨料流加工法去除內孔氧化皮,獲得了較為理想的加工效果,且磨料粒度對表面的加工質量至關重要。通過試驗與研究得出以下結論:
1)將碳化硅磨粒作為黏彈性流體磨料介質應用于磨料流加工中,加工質量較高,且可有效去除內孔表面的氧化皮。
2)采用的黏彈性碳化硅磨料粒徑應與被去除氧化皮表面相匹配,若去除氧化皮較厚且表面較祖糙的毛坯面,應選用較粗氮化硅磨粒;若去除氧化皮較薄且表面較光滑,則需選用超細碳化硅磨粒。
3)隨著氧化皮的去除,滾子內孔表面粗糙度顯著降低。若延長加工時間(增加加工循環(huán)次數)并選擇合適的粒度,內孔表面粗糙度完全可以實現納米級的精密加工。
4)利用磨料流加工法去除空心滾子內孔氧化皮,由于黏彈性磨料在出口處的突然擠入和釋放時形成的擠壓壓力過大,從而導致“喇叭口”現象的形成。在擠壓過程中增加磨粒流回程壓力,可以有效抑制“喇叭口”的形成。
5)與傳統(tǒng)手工和噴砂加工法相比,采用磨粒流加工方法去除氧化皮在經濟性、加工質量、綠色加工等方面的優(yōu)勢更顯著。
(參考文獻略)
文章發(fā)表于2022年2期《軸承》
引文格式:
于吉鯤,孫旭,吳鳴宇.利用磨料流去除空心滾子內孔氧化皮的試驗研究[J].軸承,2022(2):39-43.
軸研所公眾號 軸承雜志社公眾號
營銷熱線
0379-64367521
0379-64880626
13693806700
0379-64880057
0379-64881181